sustainability
Coopers has adopted world-best practices in the areas of energy recovery, power generation, water usage, recycling and efficient operation.
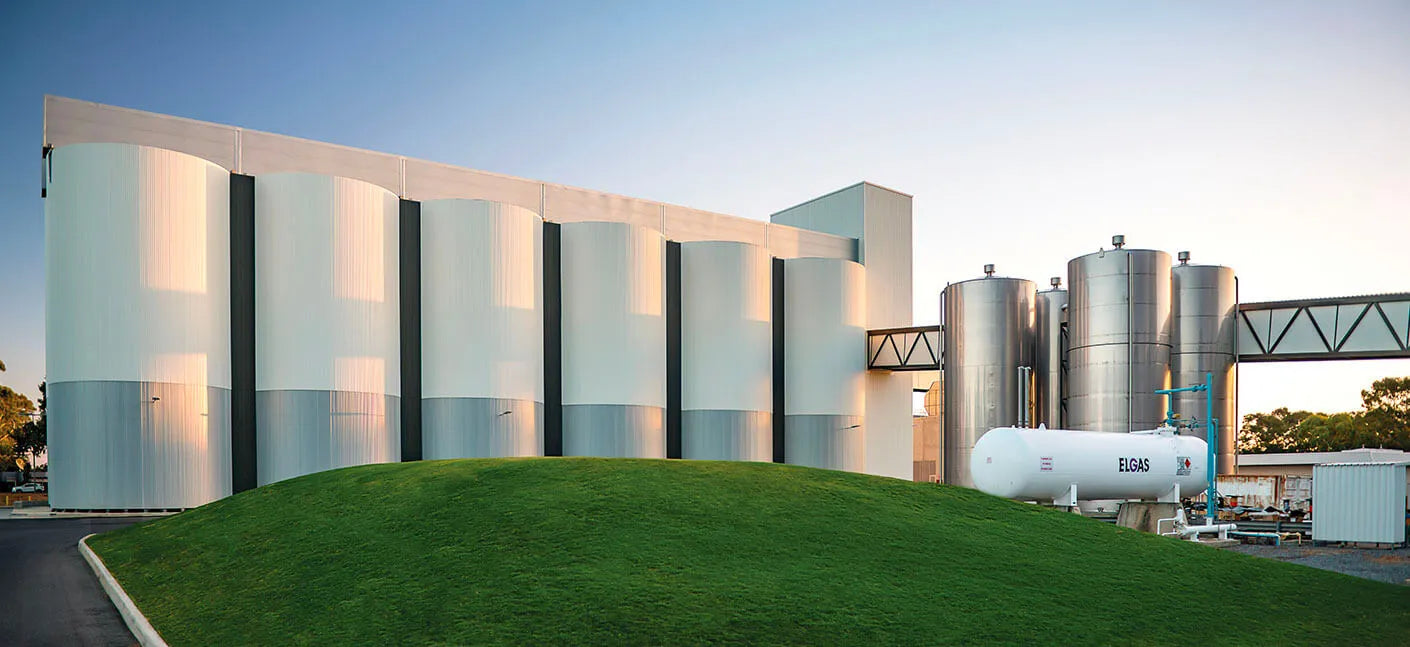
The cogeneration plant produces 12,000 megawatt hours (MWh) of power per year.
All Coopers’ electricity and steam requirements are drawn from a 4.4 megawatt (MW) natural gas-powered cogeneration plant located on site.The plant, built in partnership with AGL, burns natural gas in a turbine to drive an electricity generator, and uses the waste heat to produce steam used in the brewing and malting process. The plant also generates 50,000 tonnes of steam a year, used for heating in brewing and production processes, and for pre-heating in the maltings kiln.
COGENERATION PLANT
80%
Energy use efficiency
The plant achieves an energy use efficiency of 80%, which is approximately 2.5 times greater than a conventional power station.
15,000Tonnes
Reduced C02 emissions
This has reduced carbon dioxide emissions by up to 15,000 tonnes per annum compared with a conventional power plant.
12,000MWH
Power generated per year
The cogeneration plant produces 12,000 megawatt hours (MWh) of power per year for the brewery and the maltings.
MALTINGS
The plant can produce more than 54,000 tonnes of malt a year.
Coopers began producing DIY beer kits back in the early 70’s when legislation was changed to allow brewing at home. Initial kits were 20 litre “bag in a box” wort packs with the beer being brewed in the bag.
Water used in steeping comes from the purified water from the saline aquifers. Unique custom designed features have allowed Coopers to reduce steeping times, water usage and kiln-gas during the malting process. Power is drawn from the cogeneration plant.
PRE-STEEPING
Coopers Maltings employs a unique barley wetting screw, that was designed in-house, to wet the grain and remove contaminants from barley
The damp grain is then allowed to rest under controlled conditions for two hours. During this time, the moisture content rises from 10% to 25%, allowing shorter steeping times, more vigorous grain for germination and the possibility of single steeping under certain circumstances, thereby saving water.
KILN PRE-HEATING
The cogeneration plant produces steam from the gas turbine waste heat.
A new heat exchanger has been installed to convert surplus steam into hot water, which is used to pre-heat kiln air. This ‘free’ energy reduces gas consumption in the kiln by up to 40%.
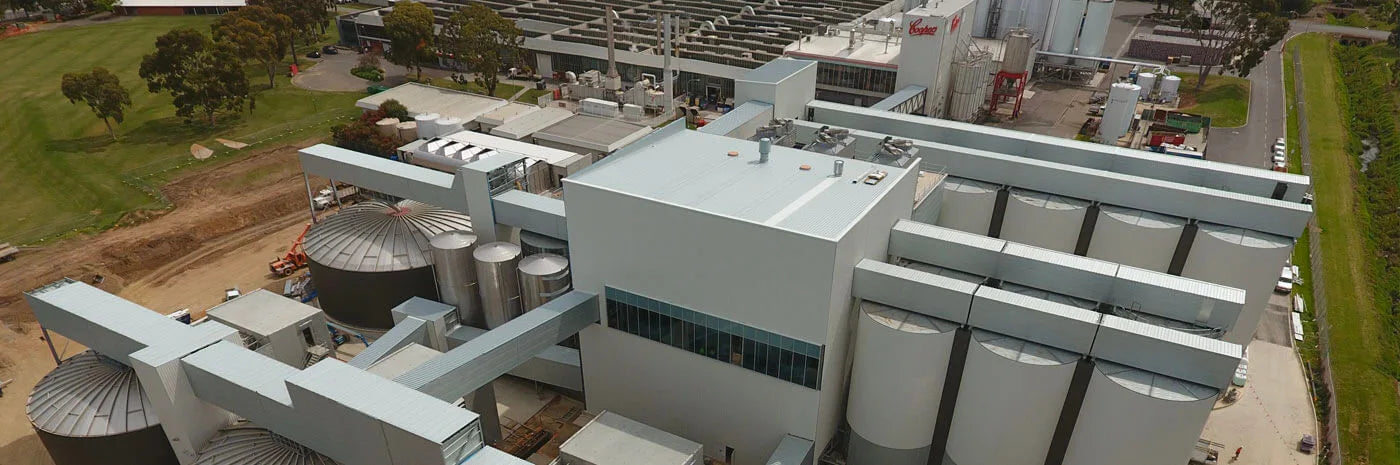
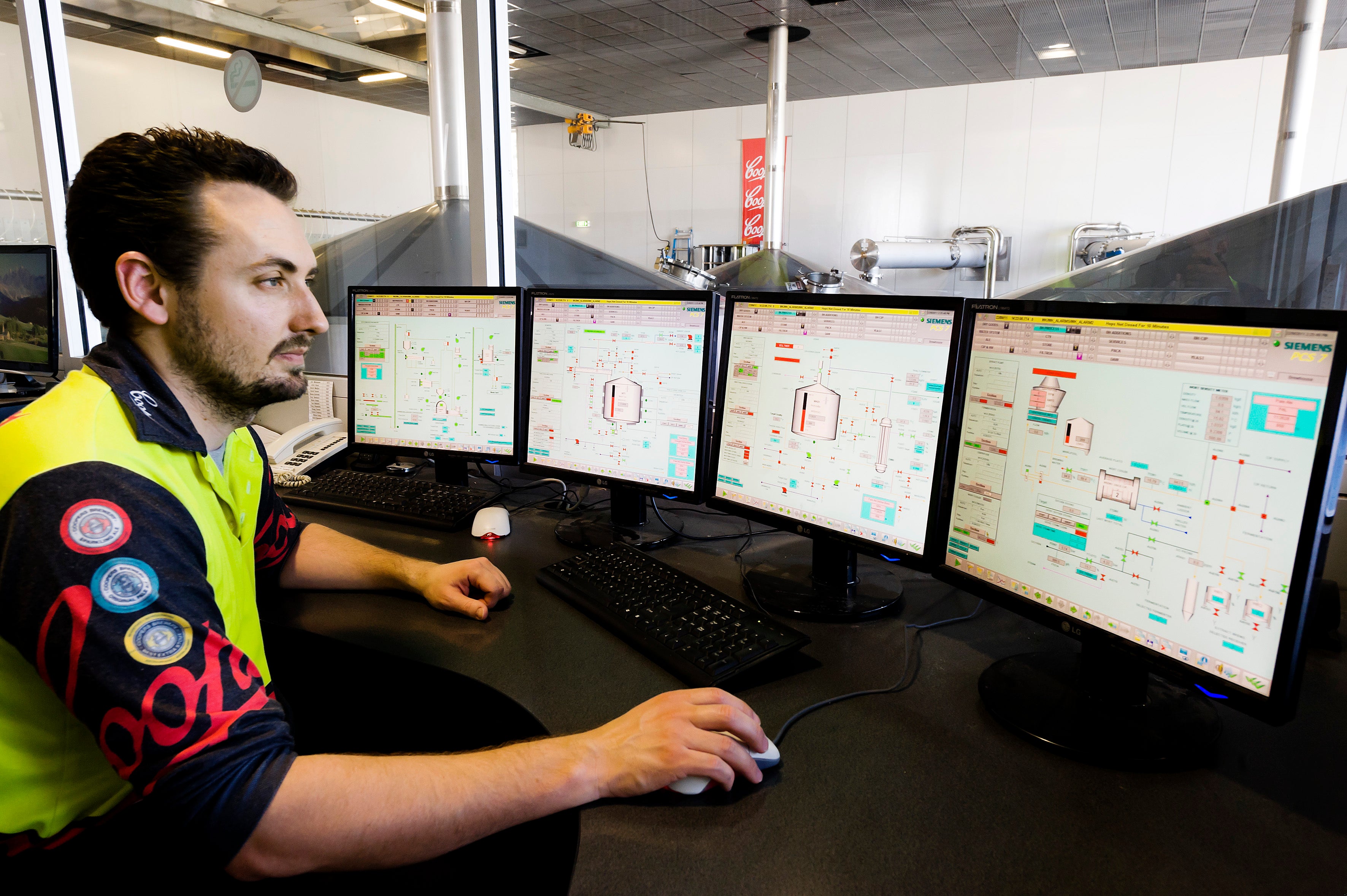
Coopers’ extensive monitoring systems help to maximise efficiency and reduce waste.
operations management
01
A sophisticated brewery-wide Supervisory Control and Data Acquisition (SCADA) monitoring system collects a broad range of information that is used for this process control and monitoring. It allows all aspects of brewing and evaporation of product to be optimised.
02
Energy audits have resulted in the installation of high-efficiency, low-energy lighting in all areas of the brewery, while condition monitoring of machinery determines the need for intervention to improve efficiency or, alternatively, replacement with more modern and effective equipment.
03
All fluid wastes are monitored for temperature, pH levels and conductivity to ensure they meet appropriate standards as part of Coopers’ trade waste licence with SA Water.
- Choosing a selection results in a full page refresh.
- Opens in a new window.